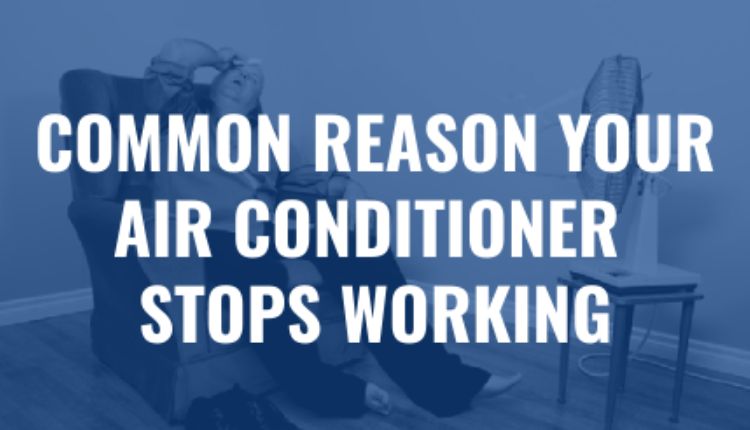
As an air conditioning company in West Berlin, NJ, we often receive calls from homeowners alarmed by their air conditioning units not blowing cold air, or making strange noises. There are several possible causes to these issues, and in this article, we will cover two of them: compressor failure, and refrigerant leaks.
We will also cover how we track and identify them, and what we do to repair them. Hopefully, this will be informative, and you will know what your technician is doing when repairing your AC unit.
Compressor Failure
Often referred to as the “heart” of the air conditioning system, the compressor circulates refrigerant throughout the system. Failures often stem from electrical problems like short-circuiting or power surges: they burn wiring and connectors, and create motor damage. Mechanical issues include bearing failure and internal component wear due to inadequate lubrication or refrigerant issues. Incorrect refrigerant charge, either too high or too low, stresses the compressor. Over time, this causes overheating and mechanical breakdown.
On a routine maintenance call, the HVAC technician performs several key checks to ensure the compressor operates within factory specifications.
- Visual Inspection: Our NATE-certified technician begins with a visual inspection of the compressor and its surrounding area, checking for obvious signs of wear, damage, oil leaks, and corrosion. He also inspects the insulation on the compressor wiring, looking for signs of deterioration.
- Refrigerant Levels: Our technician then measures the refrigerant levels to see if they are within the specified range. When too high or too low, refrigerant causes the compressor to overwork, leading to potential failure. Also, if the level is low, it is the sign of a leak as the refrigerant circuit is closed and its internal pressure should not vary when in operation. This needs to be fixed right away. An AC system with a low level of refrigerant will not blow cold air.
- Inspection and Cleaning of Coils: Our technician inspects the condenser coils, which you can see around the compressor on your AC unit. We need to remove dirt and debris, and observe signs of damage or corrosion. When coils are too dirty, the compressor will overheat and also work extra-time to achieve the desired temperature inside. This will shorten its lifespan.
- Electrical Connections: Then he checks all the electrical connections, looking for loose and corroded terminals. These must be clean and tight.
- Voltage and Amperage of the Motor: Using a multi-meter, our technician measures the values of the electrical current output by the motor of the compressor, checking whether they are to factory specifications. Deviations indicate potential problems.
- Capacitor: Start and run capacitors set the compressor in motion. These are high-discharge components which wear out relatively quickly, especially on single-speed AC units. Our technician tests the values of the output and verifies the capacitors have not lost their charge capacity.
- Unusual Noises: While the AC is running, our technician listens for any unusual noises. Noises like grinding, hissing, or a loud humming point to internal problems with the mechanical components of the compressor.
- Temperature and Pressure: Our technician also measures the temperature and pressure of the compressor. Abnormal readings can point to a refrigerant problem, airflow blockages, or a mechanical failure. We need to act quickly on these because replacing a part doesn’t cost that much, but replacing a compressor is a big ticket item.
- Safety Controls: Many compressors have built-in safety controls like pressure switches and thermal overloads. Our technician checks that these controls function correctly and have not been tripped.
- Lubrication (If Applicable): Some compressors require lubrication for smooth operation. Our technician will lubricate parts as per manufacturer’s guidelines.
Refrigerant Leaks
Refrigerant is the “lifeblood” of an air conditioning system. It is a low-temperature gas in liquid form that circulates throughout the system in a closed circuit. Any refrigerant leak will lower the efficiency and cooling ability of the system by reducing its ability to absorb and expel heat, forcing the compressor to work harder, and increasing the risk of overheating and mechanical failure.
Leaks typically occur in the evaporator or condenser coils, and at connection points. Corrosion of the coils or refrigerant lines is usually due to chemical exposure and environmental factors. This process creates weak points where leaks develop. Vibration and thermal expansion can also loosen joints over time.
To trace refrigerant leaks in an HVAC system, our technician will typically perform the following steps until the leaks are found:
- Initial System Inspection: As noted above, our technician starts with a visual inspection of the entire HVAC system, focusing on common leak points: connections, valves, and joints in the refrigerant lines, as well as the evaporator and condenser coils. Any sign of oil residue indicates a potential refrigerant leak, as the refrigerant carries oil with it throughout the system.
- Leak Detection: Our technician uses an electronic leak detector. This device is designed to sense refrigerant gases in the air. The technician passes the instrument over potential leak points, and an alarm indicates the presence of refrigerant. This is a very effective method to find small or hidden leaks.
- Ultraviolet (UV) Dye Test: This is a very common test when our technician is alerted to the existence of a leak, but can’t find it with the usual inspection methods. We inject a UV-reactive dye into the refrigerant system and run the system for a period of time. The dye circulates with the refrigerant, and will leak out at any breach points. With UV light, our technician can then visually identify the leak locations, as the dye will glow under the light.
- Soap Bubble Test: For larger or more obvious leaks, our technician can perform a soap bubble test by applying a soap solution to suspected leak areas. The refrigerant escaping from the system creates bubbles in the soap solution, visually revealing the leak location. A very simple and very effective when the leak is significant.
- Pressure Test: When the refrigerant level is very low, our technician can conduct a pressure test. First removing safely the rest of the refrigerant, the technician pressurizes the system with nitrogen. The high pressure makes leaks more detectable, either audibly as a hissing sound or visually using one of the previously mentioned methods.
Repairs and Testing
Once our technician has identified the leak, he repairs it immediately by tightening connections and replacing faulty valves as needed. Very often, the repair consists in welding the hole in the refrigerant lines. Worst case scenario, we replace damaged components like coils.
Now that the repair is done, we need to test the lines before adding a full charge of refrigerant:
- Evacuation and Recharging: Using a vacuum pump, our technician evacuates the system to remove air and moisture from it. Why? Moisture reacts with the refrigerant and the oil to create an acid that corrodes the inner side of the line. The vacuum pump pressurizes the pipes: for the test to be successful, the pressure reading must hold still. At that time, our technician will recharge the system.
- Recharging to Correct Levels: When refilling the system with refrigerant, our technician has to make sure the charge matches factory specifications. Too much refrigerant overpressures the system, and too little forces the compressor to run longer to reach the desired temperature.
- System Testing: Finally, our technician tests the system to ensure it operates correctly by monitoring the pressure and temperature readings to ensure they match specified values. With a final temperature check inside the house, our technician will confirm that the AC unit blows cold air.