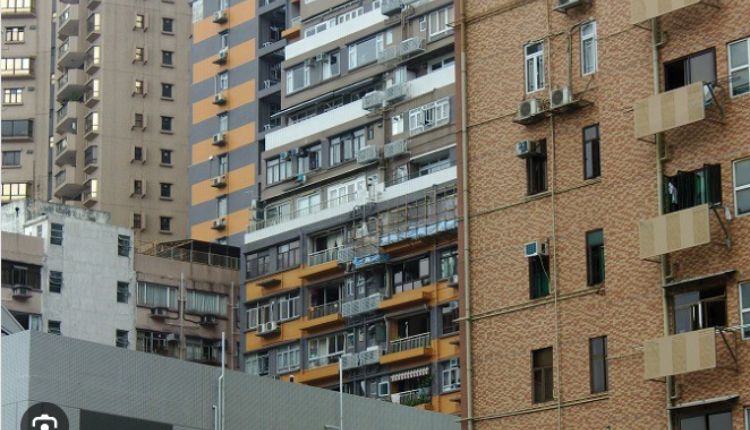
Large scale repair work is typically defined as work done to maintain equipment in a functioning condition. However, it is important to distinguish between maintenance and repair.
In order to properly perform 大規模修繕工事, an apartment should follow a long-term repair plan and have a reserve fund for repairs.
Preventative Maintenance
Preventive maintenance is a great way to keep your building in tip top shape. Whether you manage commercial, industrial or multifamily residential properties, preventive property maintenance is crucial to your success and can help you save money in the long run by reducing repairs, equipment failures, and unexpected breakdowns.
A good preventive maintenance checklist will be specific to your production assets and should always be tailored to your shop floor. Having said that, there are certain foundational elements that will be common to most preventive maintenance programs. This includes cataloging your assets, determining what maintenance items need to be done, and when to schedule those items for completion.
Identifying what assets need to be maintained can seem like an overwhelming task, especially for large operations with a diverse inventory of equipment. A helpful approach is to categorize your assets into groups that share similar maintenance needs, such as electrical or mechanical systems. From there, you can prioritize your list based on the maintenance items that require the most attention or have the highest repair costs.
The best way to ensure that your preventative maintenance program succeeds is by having a solid system for tracking the progress of each item on your checklist. This will allow you to identify when each item is finished, who completed the work and what part of the equipment was worked on. It also allows you to identify areas where more training or education is needed for your team.
Aside from the clear business benefits of routine and preventive maintenance, there are other reasons for this type of work. It improves availability, makes equipment safer for operators, encourages operator confidence and maximizes longevity. It also reduces the risk of expensive litigation.
Restaurants often feel resistant to preventive maintenance due to its complex and time-consuming nature. It feels low priority compared to the urgent need to get dinner on the tables and make sure tonight’s service goes off without a hitch. A well managed preventive maintenance process, however, can be a game changer for restaurants and make all the difference in lowering your repairs and maintenance expenses.
Reactive Maintenance
Reactive maintenance is the process of repairing assets once they have broken down and are in need of repair. This is a common approach for equipment that does not essentially influence productivity or critical tasks. The run-to-failure method is a common example, allowing a piece of equipment to be used until it begins to break down, after which a maintenance technician is called in to perform repairs and restore the asset to normal operating condition.
Reactive management requires very little planning and can be quite cost-effective for short term fixes. There are several drawbacks to this type of maintenance, however. For one, it can become very time-consuming and stressful to keep a business running smoothly when unexpected breakdowns occur. This can lead to reduced outputs, missed deadlines, and a negative impact on company reputation and revenue.
Another concern is that reactive maintenance can become very costly over the long-term if equipment fails more frequently and is repaired more often than it should be. This can lead to higher labour costs for emergency repairs and higher costs for expedited parts shipping, travel expenses and after-hours support services. In addition, systems that are patched up and repaired multiple times deteriorate much faster than those that have been properly maintained and kept in good working order.
A better solution is to combine reactive and preventive maintenance strategies in order to reduce the number of breakdowns and repair costs. This will involve a more gradual transition from reactive to preventive maintenance, but can be the best way to minimize downtime and reduce long-term costs while still ensuring that production is not interrupted.
A good tool for implementing proactive maintenance is to use work-order management software, such as Xenia, to help prioritize issues and ensure that they are being addressed. When a problem occurs, the work order is automatically assigned to the most appropriate technicians for that particular issue based on the data in your database. For instance, if the problem is electrical or plumbing related, it will be assigned to an electrician or plumber. The resulting work will then be tracked and recorded to ensure that all maintenance is being done and that there are no gaps in coverage.
Repair
Repair is a process that restores deteriorated parts of a structure to their original use potential. This is typically done to extend the expected service life of buildings and to comply with conservation rules. It also contributes to the sustainability of building resources and to the conservation of monuments. However, it is important to understand the impact of repairs on the structure durability.
In engineering terms concrete repair durability (CRD) means the additional construction service life gained as a result of successful repairs. This service life is determined thermodynamically by the structure striving to reach a condition of energy minimum and entropy increase.
When repairing concrete, the most important factor is adhesion between the new and existing materials. This can be achieved by the use of a bond coat made from equal amounts of sand and cement that is spread on the surface to be repaired and has a consistency similar to whipped cream. Alternatively, epoxy resins can be used to achieve this.
Another important factor is to select the correct type of concrete for the repair work. It should be a dense, well-graded aggregate with low water absorption and free of voids or blisters. The strength of the concrete should be as close to that of the surrounding concrete as possible. Lastly, it is essential to use a compatible curing agent.
The repairs of large concrete structures should be done by experienced and qualified engineers who are familiar with the procedures for concrete placement. For smaller repairs, it is advisable to use concrete repair mixes that are compatible with the existing concrete. For the larger areas, it is important to sound the concrete to determine the boundary of the repair area and to avoid damage to the remaining concrete. A contractor should be hired to do this.
Large-scale renovations in apartment buildings require a lot of money. It is therefore crucial to plan ahead and create a long-term maintenance and renovation strategy. This will help to save money in the long run and prevent future large repair costs. Additionally, a reserve fund should be established to cover unexpected expenses. This is important to ensure that the building is maintained to a high standard and will be safe for residents to live in.
Replacement
If the damage to a structure is so severe that it can no longer be safely repaired, then it may need to be replaced. This can be done with a similar type of structure or it can be replaced with a new one. For example, if an older concrete building was damaged in an earthquake, it could be replaced with a new concrete building. This type of 大規模修繕 work would be considered construction rather than maintenance, because it involves a significant amount of time and materials.
The actual repair costs (ARCs) at the component level are difficult to predict, especially for RC buildings because they are reported on a quote-by-quote basis in quotes submitted to funding applications. This study analyzed the ARCs for a subset of 120 RC buildings grouped in three usability classes assigned in the reconstruction process and found that the frequency distribution of the ARCs satisfactorily matches a normal distribution, with a mean value close to the actual average cost.
It is possible to use this information to benchmark loss predictions against the actual cost data and to propose reliable consequence functions calibrated on the actual repair costs of different DSIPs. The results show a clear reduction of repair costs with increasing damage extents and demonstrate the effectiveness of the proposed trilinear function.
A typical method for replacing damaged or deteriorated areas of concrete in horizontal slabs is by bonding the replacement area to the existing concrete using a layer of “bond coat.” This is typically a mixture of portland cement and sand with the consistency of whipped cream. The coating should be applied to the surface of the existing concrete before placement of the new concrete. This will create a strong bond and prevent the corrosive effects of water from penetrating through the damaged or deteriorated concrete.